Can this revolutionary plastics-recycling plant help solve the pollution crisis?

A world-first facility has a new way to break down ‘unrecyclable’ plastic waste
The world is miserable at recycling plastics. Currently, just 10–15% of the plastic waste we generate annually is recycled — with the rest incinerated, buried in landfill or dumped as litter1,2.
A big part of the problem is that much of the waste is a dirty jumble of different plastics contaminated with food, inks and labels. It’s expensive to clean and sort this mess into streams of single-polymer, uncontaminated plastic — the kind that is generally needed for conventional ‘mechanical’ recycling, in which plastic is shredded, melted and re-formed into pellets, ready for new products.
That explains the excitement around a chemical plant that will start commercial operations this year in northeast England. In principle, it can take any kind of plastic waste, including mixed plastics deemed ‘unrecyclable’, and break it down into chemicals that are similar to those extracted from crude oil. With further processing, these chemicals can be turned back into fresh plastic. If successful, it could be a powerful example of a circular manufacturing process — in which plastic is used and reprocessed over and over again — potentially curbing the world’s dependence on fossil resources to make virgin plastics.
The facility, near Redcar, uses a variation on a concept called chemical recycling, which breaks plastics apart into smaller chemical building blocks. Its main rival in this approach is pyrolysis: heating plastics to temperatures above 450 °C in a reactor without oxygen. But pyrolysis is energy-intensive and inefficient, with much of the plastic being turned into useless sooty char.
By contrast, the new plant uses water at high temperatures and pressures to break down plastic waste more gently and cleanly. Mura Technology, the London-based company behind the facility, says it is the first commercial-scale plant in the world to recycle plastic in this way. There’s a lot riding on its success — if it all works and runs profitably, it could trigger the launch of many more of these plants around the world.
Mura has declared the technology to be “revolutionary” because it “has the potential to help eliminate plastic waste, recycling all types of plastic to create a true circular economy”. Mura says that its process has lower carbon dioxide emissions and a higher tolerance for contaminated waste than does pyrolysis. It also emits roughly 80% less CO2 than burning the plastic in an incinerator to generate energy — a common way of dealing with waste.
If that makes it sound like a panacea for plastics recycling, think again. In practice, as Mura explains, the plant is currently picky about its diet of plastic waste, which must be shredded and sorted in ways similar to those used for mechanical recycling. And because, as with pyrolysis plants, not all of the facility’s products will be reborn as plastic, some critics say that the process shouldn’t count as recycling — an accusation that Mura rejects.
These practicalities raise questions about the future of plastics pollution and whether chemical recycling can live up to its promised potential. The idea is not a dud — but the real-life complications around the process make it less revolutionary than claimed.
Plastic world
Plastics pollution is a serious and growing problem. Recycling technologies already struggle to cope with today’s waste, and the Organisation for Economic Co-operation and Development (OECD) expects1 plastic-waste production to balloon to more than one billion tonnes per year by 2060 (see ‘Where plastic waste goes’).
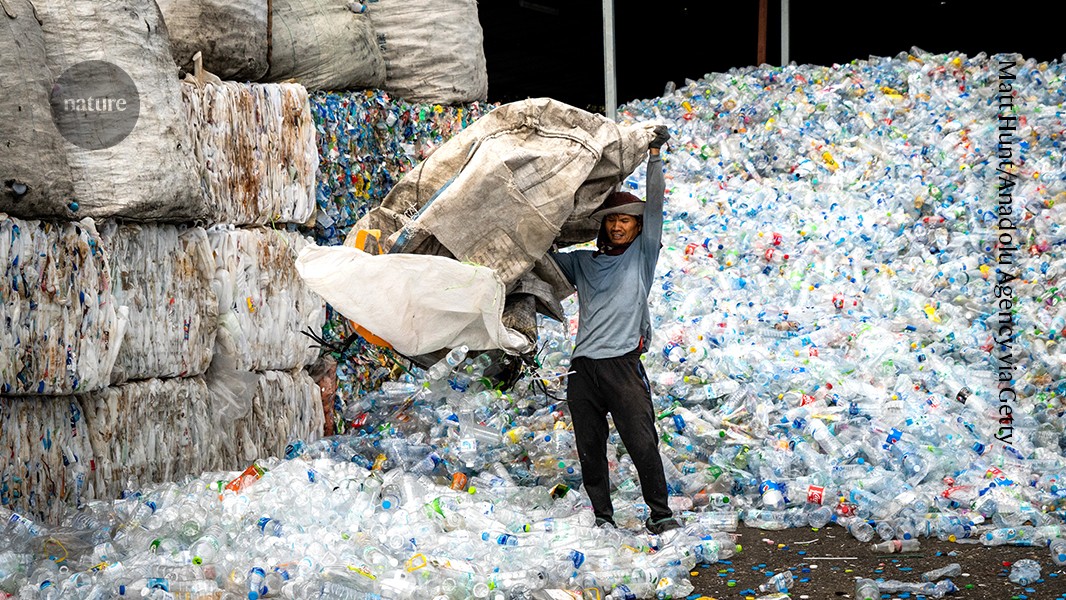
Source: OECD
Mechanical recycling is the most common recycling route. Although the process often yields a material that is a little weaker than virgin plastic, it works well enough for pure streams of some plastics, such as the polyethylene terephthalate (PET) in drinks bottles.
But other forms of plastic waste are much more challenging. Take flexible packaging and films, for example, a category that includes detritus such as grocery bags, bubble wrap and snack wrappers. These are typically made from various forms of polyethylene and polypropylene, part of a broad class of polymers called polyolefins, which make up two-thirds of all post-consumer plastic waste (see ‘Types of plastic’).

Source: Plastics Europe
These materials might be combinations of several plastics — a pain to recycle. It can be extremely difficult to tease apart mixed plastics. If they are recycled, they often result in low-quality materials that might be suitable only for making rubbish bags, offering recyclers little financial incentive to accept such waste streams.
This is just one reason why about 40% of plastic waste is put in landfill instead, with another 25% incinerated for energy recovery. About 15% is abandoned as litter2.
It also helps to explain the surging enthusiasm for chemical recycling. Many researchers, companies and policymakers think that this approach could extract more value from tricky plastic waste and thus provide an incentive for recycling3.
The current most-used chemical recycling methods, according to data from market-intelligence company IDTechEx in Cambridge, UK, involve unpicking a plastic’s polymer chains to recover the constituent chemical building blocks, or monomers. This can be done with solvents or enzymes; IDTechEx terms the general approach ‘depolymerization’. However, these are expensive processes that have been commercialized for only a handful of plastics that have already been separated from other plastic waste.
By the end of this year, IDTechEx expects depolymerization to be overtaken by pyrolysis, a blunter method. Pyrolysis does not break plastic down into its monomers — instead, it produces a soup of hydrocarbons called pyrolysis oil, similar to crude oil. Some components of this oil then go through more petrochemical processing to generate specific plastic-feedstock chemicals such as ethene and propene, the most common monomers of polyolefins.
There are roughly 50 pyrolysis plants around the world, most in the European Union and the United States, with a combined processing capacity of about 266,000 tonnes per year, according to IDTechEx. That’s a tiny fraction of the plastic waste generated in these regions. However, many more pyrolysis plants are expected to come online by the end of this year.
But pyrolysis has a number of problems. First, some of the oil it produces is turned into fuel or other chemicals, rather than going to make new plastic, so that portion doesn’t help to reduce the amount of new plastic produced. Critics such as the Brussels-based campaign group Zero Waste Europe (ZWE) say that the approach should therefore be termed ‘chemical recovery’, rather than true chemical recycling of plastic (see go.nature.com/4hjfk7z).
Second, it’s an inefficient process. Up to 20% of the carbon from the input plastic becomes an unwanted sooty by-product called char, some is lost as CO2, and the pyrolysis oil can contain contaminants that must be removed before further use4.
Third, despite their reputation for being able to feed on many kinds of mixed plastic, in practice, pyrolysis plants take in polyolefin plastic waste — and relatively clean waste at that. The reason is that this kind of waste yields a more commercially saleable pyrolysis oil that is relatively simple to drop into existing petrochemical processes, says James Kennedy, a technology analyst at IDTechEx. Different plastics, such as PET, could be pyrolysed — but they’d introduce oxygen atoms that would carry through to the pyrolysis-oil product and would have to be removed later. Meanwhile, dirtier waste tends to produce dirtier pyrolysis oil, which also has to be cleaned. To avoid that expense, pyrolysis plants still sort and clean plastics beforehand, often with the same pre-treatment steps used at mechanical recycling facilities, says Corinne Scown, a sustainability researcher at the University of California, Berkeley. Consequently, manufacturing plastic in this way costs more than mechanical recycling, and more than making virgin plastic from fossil oil.
Chemical recycling, but better?
That’s where Mura’s technology comes in. The method is known as hydrothermal liquefaction, but the secret sauce inside Mura’s stainless-steel reactor is not merely hot water. The process operates at more than 400 °C and 220 atmospheres of pressure, which means that the water is in a supercritical state — it can behave like both a liquid and a gas, dissolving oily polymer molecules and chopping them into pieces. “On the face of it, it’s quite promising. I think that there’s a lot of excitement. I’ve been to quite a few conferences where everyone’s talking about it,” says Kennedy.
Just like pyrolysis, hydrothermal liquefaction uses heat to break the strong carbon–carbon bonds that hold polymer chains together. This produces molecular fragments with an unpaired electron on each of the sundered carbons, called carbon radicals. During pyrolysis, these reactive radicals zoom around like a frenzied swarm of cannibalistic piranhas, tearing each other into smaller pieces. But in Mura’s hydrothermal process, the molten polymer is dispersed more evenly through supercritical water. This makes heat transfer more efficient, and ensures that the carbon radicals tend to sate their hunger for other atoms by plucking hydrogen from surrounding water molecules, forming more-stable hydrocarbons and avoiding char formation5.

A new plastics recycling plant near Redcar, UK, which owners Mura say will start operating in 2025.Credit: Kim Walker/Mura Technology
Supercritical fluids are already used in a wide variety of industrial processes, from purifying pharmaceuticals to decaffeinating coffee. Other companies are using hydrothermal liquefaction to convert biomass into fuels and to recycle cotton–polyester textiles.
But Mura says that this is the first time supercritical water has been applied to commercial-scale processing of waste plastic. For now, it doesn’t have much competition, although plenty of researchers are studying supercritical liquids to break down various polymers6.
Mura says that its process generates an output that is similar to pyrolysis oil, but with lower CO2 emissions, higher efficiency and a somewhat greater tolerance for contamination. Overall, Mura predicts that this will give its process an edge over pyrolysis, and thus boost recycling of mixed waste. “If this process is more tolerant to contamination, then that could put it at an advantage,” says Scown.
Black gold
Mura’s technology has been brewing for a long time. It originated with Thomas Maschmeyer, a chemist now at the University of Sydney in Australia. In the 1990s, when he was at the Technical University of Delft in the Netherlands, a company sought his advice about using supercritical liquids to process municipal waste. Although the process didn’t thrive, the concept stuck in his mind.
Years later, in Australia, he and fellow chemist Len Humphreys designed a reactor that used supercritical water to transform waste biomass such as wood chippings and agricultural residues. The pair set up a company called Licella to develop that process, called catalytic hydrothermal reactor or Cat-HTR. Along with supercritical water, Cat-HTR can use catalysts to help remove oxygen atoms from woody polymers such as cellulose, producing an oily output7. In collaboration with Canadian forestry company Canfor, Licella has just finished building a facility in Prince George, Canada, that will turn forest waste into aviation fuel.
In 2016, an investor in Licella, Steve Mahon, suggested that researchers try feeding the reactor with waste plastic. The process worked — even without catalysts — and Mahon and Licella formed Mura to commercialize it as hydrothermal plastic recycling technology (Hydro-PRT). Mahon, now Mura’s chief executive, says that the process has evolved a lot since those early trials; much of the funding for development has come from petrochemical giants such as the multinational Dow, and the US technology and engineering company KBR. “Turning something that was a lab curiosity into an industrial process has been what we’ve spent the best part of US$200 million and seven or eight years doing,” he says.
It takes about 30 minutes for Mura’s reactor to turn a batch of plastic into the desired blend of hydrocarbon products, unlike pyrolysis, which can take many hours. After depressurization, these hydrocarbons are separated from the water and then distilled into four products: naphtha, two kinds of ‘gas oil’ and a ‘heavy residual oil’ (see ‘How to recycle plastics with superheated water’). Most of the contaminants from the plastic remain in the water — unlike in pyrolysis — which means that the reactor can tackle dirtier waste without defiling its products.

Source: Mura Technology
The heavy residual oil can be used as an additive for asphalt. Naphtha and distillate gas oil are sent to Dow, which uses huge chemical reactors called steam crackers to convert the material into various products, including ethene and propene, the building blocks of new polymers. And the remainder goes to a Finnish plant, operated by oil-refining company Neste, where it goes through further refining to make various chemicals.
Just as with pyrolysis, critics such as ZWE complain that some of the plant’s output won’t be reborn as recycled plastic. And even the naphtha that goes into Dow’s steam crackers is mixed with fossil-fuel-derived naphtha before its products go to make fresh plastic. Scown points out that the supply of recycled naphtha is tiny compared with the amount of fossil naphtha processed by petrochemical plants, so that kind of mixing is inevitable to use the recycled material in existing refineries.
“From the outside, it looks like we are working towards more circularity. In reality, we are locking ourselves into keeping on using virgin plastic,” says Lauriane Veillard, a chemical-recycling policy officer at ZWE. Mura rejects ZWE’s argument that its process should be termed ‘chemical recovery’. It says that ‘chemical recycling’ refers to processes that break down waste into raw materials, which might then be used to make not only new plastics, but also other products.
Although Hydro-PRT can chew up pretty much any kind of plastic, in practice, its diet will be restricted to waste that yields the hydrocarbon products that its customers want. “We’ve concentrated on polyolefins, because we get the best-quality product for a steam cracker,” says Mahon. This also means that Mura will use many of the same shredding and sorting steps used by pyrolysis plants and mechanical recyclers to tidy up its plastic feedstock.
Still, the company insists that it will only reprocess plastic waste that has already been rejected during mechanical recycling, and would otherwise be destined for incineration or landfill. There’ll be plenty of that waste available for the facility, because a UK law requires all local authorities to collect plastic films and flexible packaging from households for recycling from April 2027.
Environmental questions
Is all this good for the environment? Stuart Coles, a sustainability researcher in the Warwick Manufacturing Group (WMG) at the University of Warwick, UK, has carried out an independent life-cycle analysis (LCA) of Mura’s process, in a study funded by the government body Innovate UK8.
It found that Hydro-PRT emitted a little under half a tonne of CO2 per tonne of waste plastic. Much of that comes from the electricity used for separating and sorting the plastic waste, along with some electrical heating, so the emissions should decline as the UK electricity grid gets greener.
The emissions are much lower than incineration for energy recovery, which belches about 2.3 tonnes of CO2 per tonne of plastic, and they are less than half of the emissions associated with refining fossil oil to create virgin naphtha. But Hydro-PRT’s CO2 output is only slightly lower than the emissions from pyrolysis plants calculated by other studies, and actually a little higher than for mechanical recycling .
“The overriding takeaway is that if you can mechanically recycle your material, then do that. If you can’t mechanically recycle it, then chemically recycle it in the way that is most appropriate for that material,” says Coles.
Enjoying our latest content?
Login or create an account to continue
- Access the most recent journalism from Nature's award-winning team
- Explore the latest features & opinion covering groundbreaking research
or
Sign in or create an accountNature 638, 22-25 (2025)
doi: https://doi.org/10.1038/d41586-025-00293-y
This story originally appeared on: Nature - Author:Mark Peplow