Hard paths: how courage differs from bravery in science

‘If it’s easy, someone else will do it.’ Leah Ellis, chief executive of Sublime Systems, explains the challenge and appeal of slashing carbon emissions from cement production
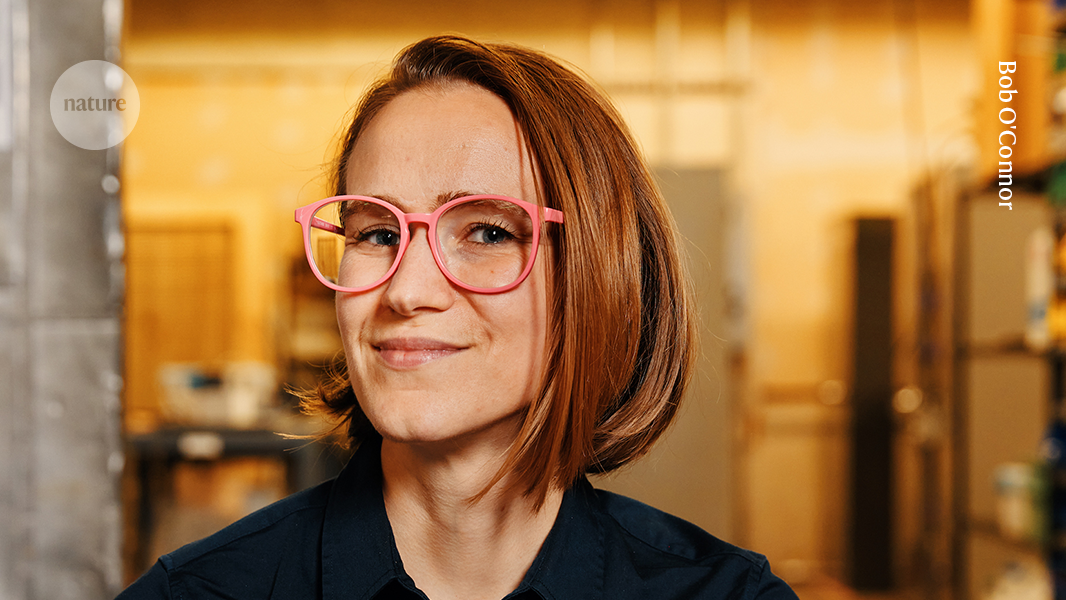
Leah Ellis co-founded Sublime Systems in 2020. Credit: Bob O'Connor
Sublime Systems, based in Somerville, Massachusetts, seeks to produce cement without using combustion, to cut down on energy use and pollution.
Leah Ellis, its chief executive and co-founder, talks about how to solve problems by working backwards, why choosing the harder career path often appeals and how courage differs from bravery in science entrepreneurship.
What pivotal moments have you had in your entrepreneurial career?
In 2018, I was awarded a Banting Postdoctoral Fellowship by the Canadian Natural Sciences and Engineering Research Council. It enabled me to work with materials scientist and engineer Yet-Ming Chiang at the Massachusetts Institute of Technology (MIT) in Cambridge. When we met, Yet-Ming had already spun off six start-up companies from his research, and five have gone on to become unicorns (privately listed companies valued at more than US$1 billion). I liked his approach of developing a technology and analysing its economic viability right from its initial stages. We co-founded Sublime Systems in 2020.
Another, earlier, influence was during my undergraduate and higher degrees at Dalhousie University in Halifax, Canada. I fell into the orbit of lithium-ion-battery pioneer Jeff Dahn, who was my PhD supervisor and mentor. During my PhD, we were contracted by electric-vehicle manufacturer Tesla and the technology company 3M to do research on lithium-ion batteries and to expand their intellectual property (IP) portfolio. Jeff’s deal with the university allowed him to be funded and to work directly with industry. We got their funding; they got our IP.
It was the coolest PhD ever. We were focused on developing real-world innovations for actual companies. Few scientists get the opportunity to work so closely with industry during graduate school. I wish more universities allowed this.
How did Sublime Systems come about?
Yet-Ming has an audacious and creative way of inventing. His idea, and the mission for Sublime, was to produce cement without using combustion, through electrochemical processes. As a freshly minted PhD holder, I would never have had the vision and audacity to work backwards from such a big thesis.
Can you tell us some more about the technology?
Globally, the electricity and heating sector contributes an estimated 40% to global carbon dioxide emissions. The goal is to reduce these to zero, using existing technologies including solar panels, wind turbines, nuclear, hydroelectricity and storage.
Cement production creates around 8% of CO2 emissions: half from the decomposition of limestone, and half from combustion needed to heat the kiln to 1,450 ºC. Globally, we use about 4 billion tonnes of cement a year, and each tonne of portland cement, the most common type used today, emits around 1 tonne of CO2.
Most of the CO2 footprint comes from the mineral emissions from the carbonate, as well as the fossil-fuel emissions needed to heat that limestone up to very high temperatures. Our process breaks down minerals without heat, using water splitting (into its constituents, hydrogen and oxygen). We call this process an ambient-temperature refinery for rocks. When splitting is done at a near-neutral pH, you can create a pH gradient — acid at one electrode and base at the other. We use that pH gradient to dissolve metals out of rocks, and then sequentially precipitate those metals. We can take almost any calcium-bearing mineral and dissolve and separate it into its constituent pure minerals, avoiding high temperatures. We can also avoid the mineral emissions from limestone, because we can use minerals such as silicates and others that aren’t bound with CO2.

Sublime Systems makes cement without using conventional combustion techniques.Credit: Mikhail Glabets
The hardened state of the concrete is the same as portland and Roman cement (the type developed in the eighteenth century, which resembles mortars used by the Romans), with similar strength and durability, engineered to have the same properties in the field but without the emissions.
What is your underlying philosophy as a science entrepreneur?
‘If it’s easy, someone else will do it.’
I’m driven by US president John F. Kennedy’s 1962 Moonshot speech at Rice University in Houston, Texas, when he said: “We choose to go to the Moon. We choose to go to the Moon in this decade and do the other things, not because they are easy, but because they are hard.”
At university, I wanted to really get my money’s worth by doing something hard, by learning something I couldn’t have figured out on my own or through a book. I majored in chemistry. It was the discipline that felt the hardest.
I worked my way through college in my home town of Halifax, making minimum wage as a cashier and shelf-stocker at an organic grocery store. And in 2014, between my master’s and PhD, I did the Tour d’Afrique, which is a 12,000-kilometre trip from Cairo to Cape Town by bicycle, sleeping on the ground every night — it’s something I would recommend to both best friends and worst enemies!
At Sublime, we are tackling a hard problem — pun intended — because the cement industry is one of the most difficult to approach, owing to its sheer scale. By mass, cement is one of the cheapest materials, at around $150 per tonne, so you need massive economies of scale — more than one million tonnes per year per plant — to make a healthy profit. The industry is very consolidated: a handful of big multinational companies dominates the market. So to come in as a fledgling start-up to disrupt this is ambitious.
How are you scaling up and expanding the team at Sublime?
You start with the basics. What does this technology need to get to the next level?
So, first it was scientists, to provide proof of concept. Next, we needed engineers to build a pilot plant in Somerville, just 15 minutes from MIT. Then you need business-development and operations people. We’re now at the size where you really need experienced executives who’ve run large, publicly traded companies before.
Our technology doesn’t fit squarely into cement or electrochemistry, so the team (now almost 100 full-time equivalents) is a mix of mechanical engineers, chemists, materials scientists and civil engineers. Some people know the same discipline from different angles. This contrasts with the more siloed ways of working at a university.
It has always been about finding the resources needed at the right time for the scale and maturity of the business. Being in Boston around such academic excellence (it’s home to institutions including MIT, Harvard University, Boston University, Tufts and Northeastern, for example) really lent itself to that.
Login or create a free account to read this content
Gain free access to this article, as well as selected content from this journal and more on nature.com
or
Sign in or create an accountdoi: https://doi.org/10.1038/d41586-025-01861-y
This interview has been edited for length and clarity.
This story originally appeared on: Nature - Author:Emma Ulker