World’s most porous sponges: intricate carbon-trapping powders hit the market Now, these intriguing materials are becoming commercial tools for capturing carbon dioxide and harvesting water from the air

Metal-organic frameworks were the next big thing in chemistry when they were invented more than three decades ago
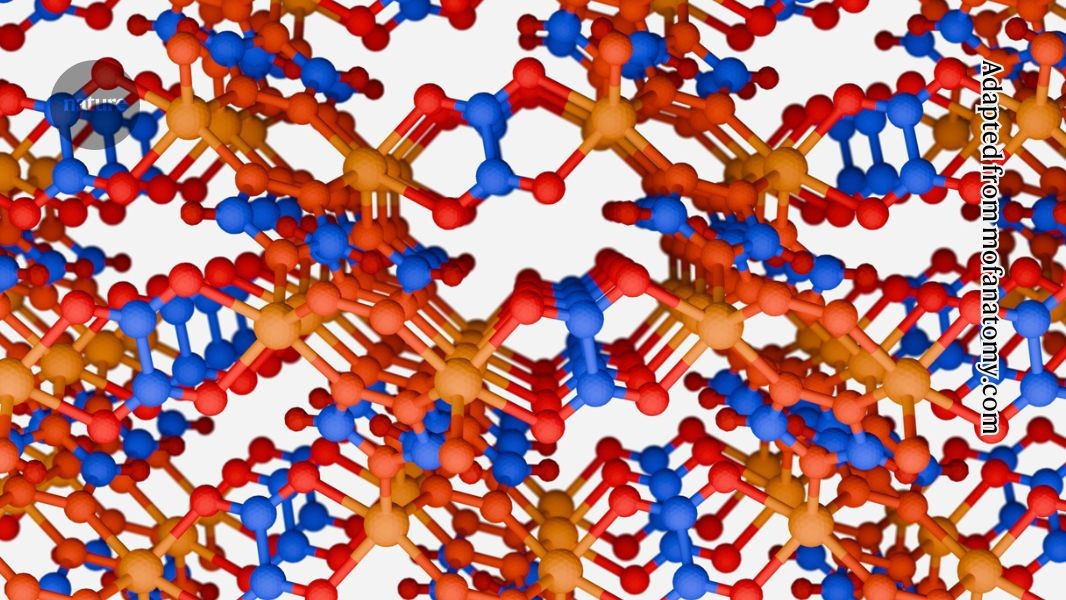
The structure of CALF-20, a metal–organic framework now made on an industrial scale to help capture carbon dioxide.Adapted from mofanatomy.com
In May this year, a US$150-million factory making filters to capture carbon dioxide opened in Burnaby, Canada. Called Redwood, after the world’s tallest trees, the facility aims to make enough filters to capture 10 million tonnes of CO2 each year, says its operator, Svante Technologies, which refers to the production line as a gigafactory.
The factory’s opening also signals a commercial breakthrough for an intriguing class of super-sponge material invented more than 30 years ago that has attracted huge academic interest and hype — but faltered commercially. Porous, powder-like solids known as metal–organic frameworks, or MOFs, have wowed academic chemists for decades.
MOFs are structured like molecular scaffolding, containing vast caverns of internal space — they are the world’s most porous solid materials. One gram of MOF powder can have an internal surface area the size of a football field.
Over the past three decades, research chemists have created more than 100,000 MOF varieties in the laboratory, and have tested the powders’ capacity to store gases, act as catalysts, trap toxic chemicals from water and deliver drugs, among many other potential uses. Scientists have also created related materials called covalent organic frameworks, or COFs. But despite huge academic interest, chemists have not managed to turn the materials into industrial-scale products.
Now, Svante and other firms have hit on the idea of using MOFs and COFs for carbon capture. One MOF is now being made on the tonne scale for use in Svante’s factory. Although it’s not clear whether these powders will actually outperform competing products — Svante’s facility also makes other kinds of material to suck up CO2 — a market does seem to be opening up, says Shababa Selim, an analyst at IDTechEX, a research consultancy in Cambridge, UK. Other firms are developing MOFs for water harvesting or filtering toxic gases. Selim suggests that the market for MOFs could grow 30-fold over the next decade, from $30 million to $930 million by 2035.
The tale of how MOFs meandered their way to a handful of industrial uses is typical of the tough reality of advanced-materials development — exciting academic inventions can take decades to find a commercial purpose. Carbon capture “seems to be the kind of breakthrough application that MOFs needed”, Selim says.
Unprecedented properties
The MOF story starts in 1989, when chemist Richard Robson at the University of Melbourne, Australia, and his colleague Bernard Hoskins announced that they’d invented “a new and potentially extensive class of solid polymeric materials with unprecedented and possibly useful properties”1. This was an early description of what would later be known as a MOF: a repeating structure built from metallic ions linked by long, rod-like, carbon-based molecules. Robson mixed copper ions with organic linker molecules he’d made; by carefully choosing the solvents and slowly evaporating them, he got these building blocks to crystallize into a porous scaffold.
In the mid-1990s, Omar Yaghi, a chemist now at the University of California, Berkeley, popularized the term MOF. Some initial structures were not stable or worked only at very low temperatures, but Yaghi developed methods to make MOFs more robust, constructing them from molecular building blocks linked through strong bonds. Academic labs leapt on the idea; more than 100,000 variants of MOFs are now recorded in the Cambridge Crystallographic Data Centre, a facility that collates structural data for molecules. And there are more than 100,000 academic papers about the materials, according to Nature’s analysis (see ‘Papers on metal–organic frameworks’).

Source: Nature analysis/Dimensions
Unlike in some porous natural materials, such as clays, the internal pores of these artificial super-sponges can be carefully and consistently sized, according to the molecules that make up the scaffolding. Researchers including Yaghi examined how MOFs could be dynamic depending on the conditions — pressure and temperature can be altered to allow gases and other cargo both in and out of the pores.
Chemists also competed to make the material with the biggest internal surface area — a title currently held by a MOF named DUT-60, made in 2018, with a whopping internal surface area of 7,839 square metres per gram2.
All that space made potential applications seem vast. Chemists latched on to the idea that they could store, transport and release hydrogen gas, for instance. In the early 2000s, Yaghi, who was then working at the University of Michigan in Ann Arbor, showed that a zinc-based MOF could take up hydrogen3. This coincided with a move by then US president George W. Bush to invest in a ‘hydrogen economy’, in which hydrogen would replace fossil fuels. It was tantalizing to think of transporting hydrogen gas inside the MOF super-sponges, and releasing it as required. Global chemicals giant BASF was an early investor, and in 2010 said it was making MOFs on an industrial scale. (The firm declined to give details about that project.)
Today, talk of a MOF-powered transport revolution and a hydrogen economy has dwindled. Not only has hydrogen storage as a concept fallen out of fashion — displaced by the drive for electric cars and the falling cost of solar power — but it didn’t work with MOFs, partly because there are huge technical challenges around filling a MOF-containing tank with enough hydrogen efficiently and quickly, says William Morris, director of business development at the start-up firm Numat in Chicago, Illinois, who did his PhD studies in Yaghi’s lab. The powders also seemed too expensive to make at large scales4. Existing technologies looked more attractive, Selim says.
Renewed attraction
But when the right application comes along, researchers can find ways to lower manufacturing costs. That seems to be the lesson from the carbon-capture industry’s blossoming interest in MOFs. “Sometimes, for materials, it’s just a matter of waiting for that one market opportunity to drive investment and also make it feasible to actually grow the production capacity, to bring the prices down,” says Selim.
Svante’s story illustrates this. Chief executive Claude Letourneau says that the firm had always been focused on removing CO2 from exhaust gases of industrial plants and was agnostic about how to do it. Svante was trying to develop a ‘doped’ silica material to trap CO2, but the material degraded too quickly to be practical. Letourneau approached the academic group of George Shimizu at the University of Calgary in Canada about a MOF it had developed, called CALF-20. This zinc-based material traps CO2 molecules in its pores, even in the presence of water, which is a major constituent of flue gases. (Many MOFs preferentially suck up water — another barrier to commercializing them for gas storage.)
“I said, ‘this is the material we need’,” says Letourneau. But the drawback was cost: making CALF-20 was too expensive to be commercially viable. “It’s a laboratory curiosity,” Letourneau says he thought at the time. He asked Shimizu to try to develop a simpler synthesis that could be scaled up. “He says, ‘Yeah, let me give it a crack’. And a year later, he comes back, and he has a very simple way of doing this,” Letourneau recalls. CALF-20 can be created from low-cost bulk chemicals dissolved in a mixture of water and methanol, the researchers found5.

The MOF CALF-20 as a powder, before it is used in Svante’s carbon-trapping filters.Credit: Svante Inc.
At Svante, researchers scaled up this method to create kilograms of the MOF before collaborating with BASF to develop a multi-tonne process. BASF now makes CALF-20 for Svante. A number of other firms have shifted or rebranded themselves to focus on MOFs for carbon capture, says Selim. Promethean Particles, a company that spun off the University of Nottingham, UK, in 2007 to develop nanoparticles, has pivoted into MOF development for carbon capture and storage, for instance.
And Belfast-based Nuada, which used to be called MOF Technologies, says it is also developing a carbon-capture and storage MOF-based product. Nuada is piloting carbon capture at an incineration facility that produces energy from waste (owned by UK firm Enfinium) in Knottingley, UK. As far as is publicly known, however, the BASF–Svante process is the only one making MOFs on a commercially relevant scale, Selim says.

This machine at Svante Technologies uses metal–organic frameworks to capture CO2.Caption: Svante Inc.
Other uses for MOFs
MOFs might not be suitable for all forms of carbon capture. Sucking CO2 directly from air is harder than sucking it from the exhaust gases of industrial plants, because of the lower CO2 concentration. Although Svante supplies carbon-capture materials to a direct-air-capture firm called Climeworks in Zurich, Switzerland, these are based not on MOFs, Letourneau says, but on chemicals commonly used for carbon capture, called porous amines.
However, in October 2024, Yaghi reported that his research team had managed to make a COF that did pull CO2 directly from the air — a promising development. He says that his team is simplifying the synthesis of that material and scaling it up6.
Yaghi’s team are also pushing to commercialize MOFs for harvesting water from air. It has demonstrated a MOF-based device in Death Valley, California, built from a material called MOF-303 that can suck in water vapour at low humidity7. The trick for these MOFs is that only a small temperature change is needed to release the trapped water, allowing it to be collected as the temperature dips overnight in the desert. Yaghi founded a firm called Atoco in Irvine, California, that is “testing pre-commercialized water-harvesting units” using the MOF, he says. The start-up firm AirJoule in Ronan, Montana, is also targeting direct-water capture; in June this year, it signed a deal with an unnamed developer of data centres to incorporate its proprietary MOF water harvester into those facilities.

A trial of a MOF-based water harvester in Death Valley, California. Credit: Yaghi Laboratory, Univ. California
Login or create a free account to read this content
Gain free access to this article, as well as selected content from this journal and more on nature.com
or
Sign in or create an accountNature 643, 322-324 (2025)
doi: https://doi.org/10.1038/d41586-025-02067-y
This story originally appeared on: Nature - Author:Katharine Sanderson